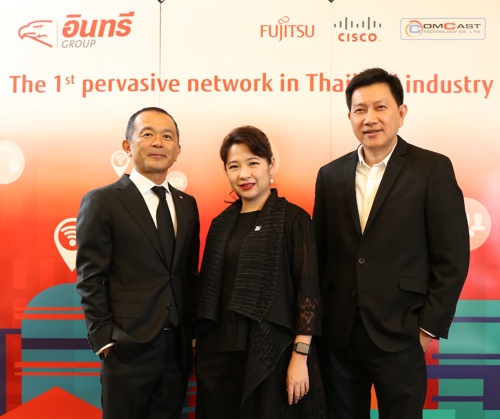
แม้รัฐบาลไทยจะประกาศนโยบาย Thailand 4.0 มาแล้วสักระยะ แต่ก็คงปฏิเสธไม่ได้ว่า ที่ผ่านมา องค์กรหรือโรงงานขนาดใหญ่นั้นมีน้อยมากที่จะออกมาประกาศตัวว่าพร้อมจะลงทุนเพื่อปรับกระบวนการผลิต หรือกระบวนการทำงานเพื่อให้รองรับกับเป้าหมายของการเป็น Industry 4.0 ที่ต้องมีการนำเทคโนโลยีเข้ามาใช้อย่างชาญฉลาด และสามารถเพิ่มประสิทธิภาพขององค์กรได้
แต่สำหรับใครที่มีโอกาสขับรถผ่านเส้นพหลโยธินข้ามจังหวัดสระบุรี เป็นไปได้ว่าคุณอาจกำลังวิ่งผ่าน “โรงงานดิจิทัลอัจฉริยะ” (Digital Connected Plant) แบบครบวงจรแห่งแรกของประเทศไทยภายใต้ชื่อ “ปูนซีเมนต์นครหลวง” ที่ตอบโจทย์ความเป็น Industry 4.0 เข้าแล้วอย่างไม่รู้ตัว
โดยโรงงานปูนซีเมนต์นครหลวงที่หลายคนคุ้นตาจากการมองผ่านกำแพงภายนอกนั้น ภายในโรงงานกำลังอยู่ระหว่างการทำ Digital Transformation ครั้งใหญ่ภายใต้งบลงทุนเกินร้อยล้านบาท (เริ่มต้นในปี 2015) โดยการทำ Digital Transformation ครั้งนี้เป็นการนำเทคโนโลยี Pervasive Network จาก Cisco เข้ามาและติดตั้งระบบโดย Fujitsu เพื่อทำให้โรงงาน เครื่องจักร พนักงาน รวมถึงบรรดา Contractors สามารถเชื่อมโยงเข้าด้วยกันได้อย่างสมบูรณ์แบบ
การติดตั้งระบบโครงสร้างพื้นฐาน
เหตุผลที่นำไปสู่ความเปลี่ยนแปลงนั้น คุณอิฑยา ศิริวสุกาญจน์ ประธานเจ้าหน้าที่บริหาร บริษัท อินทรี ดิจิตอล จำกัด บริษัทในกลุ่มบริษัท ปูนซีเมนต์นครหลวง จำกัด (มหาชน) ผู้รับหน้าที่การทำ Digital Transformation ให้กับโรงงานปูนซีเมนต์นครหลวงในครั้งนี้เผยว่า การมาถึงของยุค Digital Disruption นั้นรุนแรงมาก ซึ่งภาคการผลิตจำเป็นต้องปรับตัวและนำเทคโนโลยีดิจิทัลเข้ามาช่วยเพิ่มประสิทธิภาพในการทำงานก่อนจะถูก Disrupt นั่นเอง
ด้านคุณวัตสัน ถิรภัทรพงศ์ กรรมการผู้จัดการ บริษัท ซิสโก้ ประเทศไทยและภูมิภาคอินโดจีนได้นำผลการศึกษา Global Center for Digital Business Transformation ประจำปี 2015 มากล่าวเสริมโดยระบุว่า ภาคโรงงานการผลิต (Manufacturing) นั้นเป็นธุรกิจที่มีความเสี่ยงต่อการถูก Disrupt ในลำดับที่ 8 จากทั้งหมด 12 อันดับ ซึ่งการที่ปรากฏชื่ออยู่ตารางนี้แล้วนิ่งนอนใจอาจนำไปสู่การถูกกลืนหายได้ในที่สุด
การพลิกโฉมโรงงานสู่ Connected Plant จึงเกิดขึ้น ซึ่งหัวใจสำคัญของการเปลี่ยนแปลงนั้นประกอบด้วย 5 คีย์หลักดังนี้
หัวใจสำคัญสู่ Digital Connected Plant
- การติดตั้ง Pervasive Network ก่อนเป็นลำดับแรก เพื่อวางฐานรากแห่งการ Connected เครื่องจักร – เซนเซอร์ต่าง ๆ ให้เกิดขึ้น
- เมื่อระบบสามารถเชื่อมต่อเซนเซอร์ต่าง ๆ และระบบการทำงานของเครื่องจักรเข้าด้วยกันได้แล้ว ทีมวิศวกรของปูนซีเมนต์นครหลวงก็จะสามารถเดินตรวจตราเครื่องจักร และระบบงานต่าง ๆ ได้สะดวกขึ้น นอกจากนี้ การตรวจสอบเครื่องจักรจากเดิมที่ต้องใช้กระดาษ ก็จะเปลี่ยนเป็นตรวจเช็คผ่านแท็บเล็ต และหากมีปัญหา ทีมวิศวกรสามารถโหลดคู่มือมาดูได้จากแท็บเล็ตทันที หรือหากไม่สามารถแก้ไขได้ ก็สามารถถ่ายคลิปเครื่องจักรที่มีปัญหา ส่งเข้าสู่ศูนย์กลางเพื่อปรึกษาผู้เชี่ยวชาญทั้งในประเทศไทยและต่างประเทศได้
- มีการติดตั้งเซนเซอร์เพื่อตรวจสอบการทำงานของเครื่องจักร โดยเซนเซอร์ดังกล่าวจะคอยตรวจจับความผิดปกติตลอดเวลา และหากพบแนวโน้มว่าอาจมีชิ้นส่วนเสีย Machine Learning จะคาดการณ์ได้ว่าความเสียหายนั้นจะเกิดขึ้นเมื่อไร และระบบสามารถส่งสัญญาณแจ้งเตือนไปยังศูนย์กลางได้ล่วงหน้า ซึ่งในกรณีนี้นอกจากจะทำให้การบำรุงรักษาเป็นไปอย่างมีประสิทธิภาพแล้ว ยังสามารถลดค่า DownTime (กรณีที่เครื่องจักรหยุดทำงานแบบกระทันหัน) ให้กับโรงงานได้ด้วย
- พนักงานแบบ Contractors ที่เข้ามาทำงานในโรงงานจะได้รับเซนเซอร์ตัวเล็ก ๆ ติดที่ชุด โดยเซนเซอร์นี้จะเป็นตัวชี้ตำแหน่งของพนักงานเหล่านั้นว่า ทำงานอยู่ในจุดที่ได้กำหนดไว้หรือไม่ ซึ่งเป็นการรักษาความปลอดภัยให้กับตัวพนักงาน Contractors เอง และรักษาความปลอดภัยให้กับโรงงานด้วย
- ข้อมูลต่าง ๆ ที่ได้จาก Connected Plant จะถูกส่งเข้ามายังศูนย์กลาง ช่วยให้ผู้บริหารสามารถตรวจสอบข้อมูลได้อย่างสะดวกรวดเร็ว
คุณวัตสันเสริมในจุดนี้ด้วยว่า ในอนาคต เราเห็นเทรนด์หนึ่งที่ว่าผู้เชี่ยวชาญในภาคอุตสาหกรรมมีแนวโน้มจะหายากขึ้นเรื่อย ๆ เราจึงต้องนำเทคโนโลยี และระบบออโตเมชันเข้ามาช่วยให้วิศวกรมีโอกาสเข้าถึงคำปรึกษาจากผู้เชี่ยวชาญอย่างมีประสิทธิภาพมากขึ้นนั่นเอง
ทั้งนี้ คุณอิฑยาเผยว่า ปูนซีเมนต์นครหลวงมีโรงงานอยู่ที่สระบุรีทั้งสิ้น 3 แห่ง และการทำ Digital Transformation นี้เริ่มกับแห่งที่ 3 เป็นที่แรก โดยมีกำหนดแล้วเสร็จภายในสิ้นปี 2017 และขณะนี้ได้ทำการติดตั้ง Pervasive Network เรียบร้อยแล้ว ซึ่งเท่ากับว่าบริษัทมีเวลา 6 เดือนในการให้วิศวกรปรับตัวและเรียนรู้กับระบบดังกล่าว
ด้านคุณอิจิ ฟุรุคาวา กรรมการผู้จัดการ บริษัท ฟูจิตสึ (ประเทศไทย) จำกัด เผยว่า ที่ผ่านมา ฟูจิตสึมีการวางแผนร่วมกับลูกค้าเพื่อให้มั่นใจได้ว่าลูกค้าอย่างปูนซีเมนต์นครหลวงได้ผลลัพธ์อย่างที่ต้องการ จนนำไปสู่ความสำเร็จของการติดตั้งระบบ Pervasive Network ให้กับ Connected Plant ครั้งนี้ในที่สุด
ในฐานะที่ประเทศไทยเป็นประเทศที่มีภาคอุตสาหกรรมการผลิตใหญ่เป็นอันดับ 17 ของโลก และมีส่วนช่วยสร้างจีดีพีของประเทศถึง 32.5 – 35.6 % มาตั้งแต่ปี 2011 – ปี 2014 คงปฏิเสธไม่ได้ว่า บางทีนี่อาจถึงเวลาที่ภาคอุตสาหกรรมจะต้องก้าวเข้าสู่การทำ Digital Transformation เพื่อรองรับการแข่งขันในยุค Digital Disruption กันอีกครั้งแล้ว โดยฟรอสต์ แอนด์ ซัลลิแวน ได้มีการคาดการณ์ว่าค่าใช้จ่ายด้าน IoT ของธุรกิจในประเทศไทยทั้งหมดว่าจะสูงถึง 30,000 ล้านบาทในปี 2020 และอุตสาหกรรมด้านการผลิตในประเทศไทยจะมีค่าใช้จ่ายไปกับโซลูชัน IoT ถึง 16,000 ล้านบาท โดยคิดเป็นอัตราการเติบโตที่ 13.2 % ในระหว่างปี 2016 – 2020 เลยทีเดียว
ในสถานการณ์เช่นนี้ เป็นไปได้ว่า ผู้ที่ปรับตัวก่อน ก็คือผู้ที่จะมีประสบการณ์และพร้อมออกเดินได้ก่อนใครนั่นเอง